こんにちは。株式会社イノベーティブ・ソリューションズ(以下、ISOL)の李涵琳(リ・カンリン)です。私は中国、遼寧省丹東市出身です。学生時代に北海道大学の水産学部で食品科学を学び、食品衛生学や食品保蔵学などの授業を受けながら、干物におけるヒスタミン産生菌の汚染状況調査・水産物における過酢酸処理の抗菌効果の研究に取り組みました。
学生時代にマグロの加工過程ラインを見学した際、人が口にするまでの工程に驚いたのを覚えています。また、万が一食中毒問題が生じた際に、一連の全製品を廃棄する必要性などを考えると、商品が原材料から最終製品になるまでの製造プロセスを可視化して管理することの重要性を認識しました。「食の安全」は食品添加物などの化学方法での担保だけではなく、例えば温度管理や金属検査といったIT技術も必要になります。当時、研究室で干物について実験をする際に湿度センサーを使っており、スマートフォンを繋げてどこでもデータ監視・分析ができるようになっていました。その時からIT技術に魅力を感じるようになり、また、ISOLの国際的な雰囲気が合うと感じて2019年に入社しました。
学生時代の知識・経験と入社後勉強したIT技術を食品業界で生かしたい、ソリューションを作りたいと思っていたところで、2021年6月にHACCPが完全義務化されました。
調べていると、HACCP導入における文書化の課題、管理基準(Critical Limit:CL)のモニタリングにおける課題が発生していることが分かりました。今回ご紹介するHACCPソリューションで、安心安全で且つ効率的により良い商品を市場に提供するためのご支援をしたいと考えております。
HACCPについて
・HACCPとは
・HACCPに沿った衛生管理の制度化とは
・HACCP方式と従来の製造方法の違いは
HACCP制度化における課題
・文書化の課題
・管理基準(Critical Limit:CL)のモニタリングにおける課題
課題解決のための有効な手段
・文書化の課題解決方法とは
・管理基準(Critical Limit:CL)のモニタリングにおける課題解決方法とは
HACCPについて
HACCP (Hazard Analysis and Critical Control Point)とは?
HACCPは元々アメリカのNASAにおいて宇宙食の安全性を確保するために考案され、後に食品全般の安全性を確保するための衛生管理手法として確立された用語です。(図1)
(図1)
HACCPとは、「Hazard Analysis Critical Control Point」の頭文字をとったものであり、食品等事業者自らが食中毒菌汚染や異物混入等の危害要因(ハザード)を把握した上で、原材料の入荷から製品の出荷に至る全工程の中で、それらの危害要因を除去又は低減させるために特に重要な工程を管理し、製品の安全性を確保するための衛生管理の手法です。以下(図2)は、HACCPの手法による管理の例です。
(図2)
HACCPに沿った衛生管理の制度化とは
令和3年6月1日から、原則としてすべての食品等事業者がHACCPに沿った衛生管理に取り組むことが制度化されました。
HACCP方式と従来の製造方法の違いは
従来型の方法とは違い、HACCPは7原則12手順に沿って管理することを規定しています。―食品原材料の受入れから最終製品までの各工程ごとに、 ① 微生物、化学物質、金属の混入などの潜在的な危害要因を分析・予測 (Hazard Analysis)した上で、 ② 危害の発生防止につながる特に重要な管理点(Critical Control Point)を継続的に監視・ 記録する―工程管理のシステムです。
HACCPの7原則12手順は以下の(図3)に記載されている通りです。
(図3)
HACCP制度化における課題
文書化の課題
HACCP文書化を行う際には、ほとんどの企業で採用されているエクセルをはじめとしたオフィスツールを利用して業務プロセスの整理が行われています。特にエクセルが利用されているケースが多いようですが、エクセルは表作成には適しているものの、作図には必ずしも適していないため、以下のような文書化における課題が発生しています。
プロセス整理の煩雑性による低い効率性と生産性
まずHACCP業務プロセスの作成・整理・修正を実施する際に文書作成担当が特に苦労されているのは、工程の連番の採番、フローダイアグラムの工程間の接続線の意味付けなどの処理です。これらの細かい設定作業は文書作成担当者にとっては非常に負荷が高く、効率の悪い作業となっており、また複数の担当者で作成する際には文書の書式・粒度がバラバラになってしまうこともあり、結果として全体の業務プロセスが非常に分かりにくくなってしまうことが多くあるようです。(図1)
(図1)
HACCP文書のメンテナンス作業の属人化
一般的に製造工程全体の業務プロセスを網羅的、且つ適切に把握している人は限定されていることが多いこともあり、文書化業務も結果として特定の人物に集中してしまうことが多いようです。文書化における書式やフォーマット、作図ルールなどが確立していない場合、複数の人員で作業を分担することが困難となり、また更新などが必要になった際にも過去の文書を効果的に流用することも困難となるリスクがあります。(図2)
(図2)
HACCP文書全体の整合性の確保
業務フローに記載された各プロセスやアクティビティーと各種ハザードや重要管理点の紐づけ関係の整合性を整備・維持することはオフィスツールの機能の限界もあり、非常に困難な作業となります。(図3)
(図3)
管理基準(Critical Limit:CL)のモニタリングにおける課題
管理基準(CL)とは、製品の安全性を確保できるか否かの分岐点となる重要な値(限界値)です。管理基準(CL)から外れるなどの異変はすぐに検知する必要があるため、管理基準(CL)はリアルタイムでモニタリングする必要があります。これらモニタリング設定を行うにあたっての課題が以下の点となります。
モニタリング対象の項目が不明確
マネジメントはリスク管理の視点からモニタリング導入に積極的である場合が多いですが、現場業務に精通していないためどこから手を付けるべきかの見極めが困難となっている場合があります。一方の現場側としては、マネジメント層から指示される業務改革やモニタリング導入を迅速に行なえない場面が多くあるようです。つまり原材料受入から出荷までプロセスのどの工程をモニタリング対象とすべきか常に把握できていないことが要因です。 (図4)
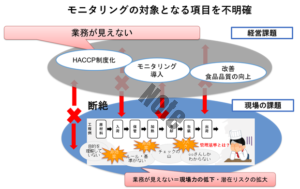
(図4)
モニタリング業務の課題
多くの製造現場では、手作業によるモニタリング業務が行われています。例えばスーパーマーケットや小売店では、冷蔵・冷凍ショーケースの温度データを手作業で紙に記録、紙のまま保管・管理されている場合が多い状況です。手作業では記録漏れや測定ミスなども起きやすく、義務を遂行する上でのリスクが高い状態となります。また管理レベルにばらつきが出てしまい、低い生産性と共に管理レベルを上げることも困難となります。(図5)
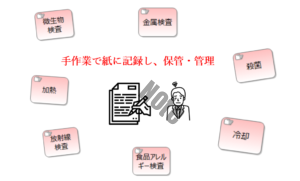
(図5)
課題解決のための手段
文書化の課題解決方法とは
文書化ツールの採用
習得難易度が低く誰でも効率的に文書化が可能となる作図ツールの利用で文書化作業の効率を高め、作業負荷を軽減することが可能です。
作図ルールの標準化
作図ルールを標準化することで誰でも統一性のある文書の作成が可能となります。担当する社員によって品質に大きな差がなくなるため、担当者以外が行った途端、大幅に時間がかかる、成果物の品質が低下する、ミスが増えるといった事態も避けられます。
文書間の関連性確保
フローダイアグラムに、製品説明書やハザード分析表、重要管理点一覧表等の外部ファイルやWeb ページとのリンクを張ることができるツールを選択することで、作図作業の効率性を高めることができます。
管理基準(Critical Limit:CL)のモニタリングにおける
課題解決方法とは
モニタリング対象となる項目を明確化
経営者と現場側がそれぞれの視点で可視化できる業務プロセスを確立します。HACCP7原則12手順を参照しながら、原材料の受入から最終製品の出荷までの一連のフロー内においてモニタリング対象となる工程を明確にし、To-Be業務プロセスを作成する必要があります。 (図6)
(図6)
IoTを活用しリスク管理
IoTを活用することでモニタリング業務を自動化することが可能です。たとえば食品製造現場やスーパーマーケットでは、冷蔵庫や冷蔵ショーケースに温度計センサーを設置し、データを自動的に取得することで記録漏れや測定ミスなどを予防することができます。また、ペーパーレス化の推進を組織全体で行い、人による手作業工数削減が可能になるほか、管理業務の効率化に役立ちます。
次回は弊社のHACCPソリューションについてのご説明と弊社が目指す目標をお話し致します。
お問合せ
株式会社イノベーティブ・ソリューションズ
info@innovative-solutions.co.jp