第3回「業務フローが無いと何が困るのか(2)」
前回のブログでは、業務フローが無いことによるプロジェクトでの困りごとについて記述しましたが、今回はプロジェクト後の通常運用に入ってからの困りごとについて記述していきたいと思います。
・・・物流部の来年度予算会議での会話・・・
役=担当役員 部=物流部長
役:倉庫管理システム(WMS)導入後もITコストが多くかかっているが適切にコストは使われているのか?
部:WMS導入後もサービスレベル向上や業務改善にかかるシステム対応が多く発生しました。
役:では、改善効果について説明してもらおう。特に対売上高物流費の今後の見通しについて聞きたい。
・・・物流部の来年度予算会議での会話・・・
部=物流部長 担=担当チーム
部:今年度のITコストだが、きちんとコスト対効果は算出したのか?
担:しました。システム化できれば工数が削減できると思われる箇所を計算の上実施しています。EXCELで案件ごとの効果予測を整理しています。
部:案件ごとに予測通りの結果が出ているのか?それに、案件ごとに具体的に何がどう変わったのかを示すドキュメントはあるのか?
物流部は(狭間の部署で)つらいよ
物流とは販売や調達の在り方に大きく影響を受けます。
中でも販売物流における倉庫はまさに販売と生産や調達の狭間に位置付けられている関係上、顧客との納品条件の変更や販売量の増減、季節変動、仕入れ先の追加など、倉庫業務には常に変化が強いられます。
そのような環境下にあって尚、物流業務の生産性向上や対売上高物流費の低減など、物流部として取り組むべきテーマが与えられ、これらを実現するためにも業務改善は継続的に行われるべき活動となります。
上記の担当役員とのやり取りからも、社内で物流部が置かれている難しい立場が推測できます。
To-Be作成の前にAs-Isの作成・分析が重要
そのような環境下にある物流現場において行われる業務改善の進められ方はどのようなものでしょうか。
私の実体験を通しても、倉庫で働く人の実務能力は海外に比べて日本が圧倒的に高いレベルにあります。
そのため、日本の倉庫現場では改善につながるヒントや提案は現場から上がってくることも多く、更には営業部門など外部からの要請等を含めると、改善ポイントを挙げたリストは、システム変更の必要性の有無に関わらず、あっという間に長いリストになります。
課題や改善点の確認には関連業務のプロセスフロー重要
私がこれまで携わった業務改善プロジェクトでは、これらの長いリストに対して、課題や解決方法、コストなどを分析した上で、優先順位の高い案件から取り組んでいくというスタイルが取られています。
この分析の過程で多くの場合不足しているのが、現状の業務の流れを記述したドキュメント「(As-Is)業務フロー」です。
第1回目に記述したように、多くの物流現場には非常に業務に精通した熟練者が存在しているため、業務上の課題について詳細を把握されています。
ただし、ドキュメントが整備されていないため、ヒヤリング後に関連業務のプロセスフローを作成し、課題を具体的に示すところから仕事が始まるということになります。
例えば倉庫業務における集品の精度の問題、フォワーディング業務におけるドキュメント作成の生産性の問題など、課題となっている業務の具体的なプロセスや、前後で行われている業務との関連性、使用されているシステムや帳票などを記述することで、課題を分析する上での見落としの可能性を低減することができます。
As-Isの業務フローの作成を怠った結果…
自己の反省を込めて、改善がうまくいかなかった経験を思い起こすと、実は「(As-Is)業務フロー」の作成を怠って先に「(To-Be)業務フロー」を作ってしまったことがあります。
つまり、現状の課題を十分に精査することなく、現状の業務を「分かったつもり」で先に進めてしまい、課題の要因に対する検討を十分に行うことなく改善後の業務プロセスを描いてしまい、結果的にはその際の見落としが理由で見込み通り改善効果が得られなかったということがありました。
改善効果を示すドキュメントの重要性
優先度が精査された上でコストをかけて行われた改善活動のあと、想定通りの効果が得られたかどうかの精査が出来ていない現場も多くあります。
冒頭のやり取りでも見られる通り、改善プロジェクトの対象となった案件ごとのビフォア/アフターが記述されたドキュメントが不足していることが多く、担当者が頭の中で把握されているだけであったり、案件ごとのコスト効果が不明確になってしまうことがあります。
改善効果の検証が行われなかった
システムベンダーに所属していたころ、倉庫業務での改善活動の一環で、一部の取引先向けに限ってピッキングの方法をオーダーごとのピッキングから、複数オーダー分を一括でピッキングする方法に変えた際のことです。
WMS(倉庫管理システム)の機能変更等もあるため、事前に業務ヒヤリングを行い概要設計して開発コストを算出した上で、想定される業務側の改善効果との比較をした結果、クライアント内で承認されたため、システム詳細設計・開発・テストし納品し、晴れて実稼働にこぎ着けました。
しかしその後、実際のところ改善効果が見込み通り上がったのか、見込み通りにはいかなかったのか、想定通り改善されなかった理由がピッキングの前工程にあるのか、使うマテハンに想定外のことがあったのかなど、具体的な検証が行われることはありませんでした。
他にも、WMSのリプレースプロジェクトを実施した後、想定通りに生産性が上がらなかったという評価をされる一方、具体的にどこの業務がどの程度生産性が上がらなかったのかを分析・検証する機会も得られませんでした。
改善効果の検証が行われない理由と重要なポイント
では、なぜ改善効果の検証を行わないのでしょうか。
その理由は、事前の課題に対する分析の方法にあると考えています。
つまり改善前の業務の流れを描いたAs-Is業務フローと、改善後の流れを書いたTo-Be業務フローがないため、具体的に何が変わったのか、前後の工程におけるどの業務で想定外のことが起きたのか、生産性が想定通り上がった工程と上がらなかった工程はどこかなど、検証する土台がない状態となってしまうことが多くありました。
このような事態を未然に防ぐためにも、やはりAs-Isの業務フローが常に用意された状況にしておくことは、プロジェクトの有無に関わらず、日々の改善活動の中でも重要なポイントとなります。
システムベンダーとして、物流コンサルタントして、過去にこれらの状況を招いてしまったことは大きな反省点として深く記憶に残っていますので、今では、何よりも先にAs-Isの業務フローを整備することが、継続的な業務改善を効果的にするためのステップだという認識をしており、その必要性をクライアントに伝え、理解を得られた上で改善の支援をさせて頂いています。
さて、過去2回のブログで業務フローの重要性について、私自身の過去の反省を踏まえて書いてきましたが、次回は業務フロー作成にあたっての人材確保・育成についての悩み事について書いていきたいと思います。
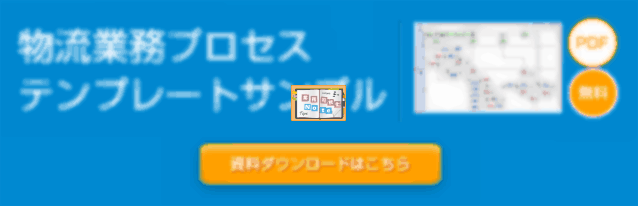