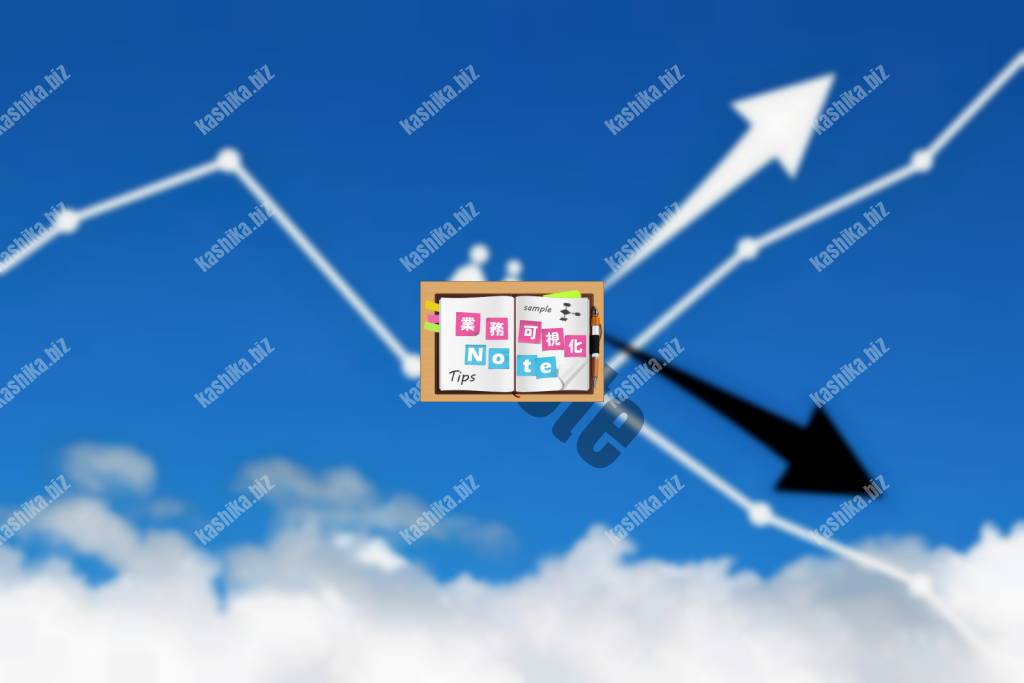
設計開発部門における技術伝承は、製造業においては特に大きな課題となっています。
これまで技術伝承に向けて様々な取り組みやチャレンジが行われてきましたが、技術伝承をうまく成功させた企業もいれば、失敗してしまった企業もでてきています。そこ明暗を分けたポイントはどのあたりにあるのでしょうか。
今回は、製造業の設計開発部門の技術伝承をサポートしている、株式会社ワイ・ディ・シー 共動創発事業本部 シニアアーキテクトの八重島師門様にインタビューを行い、熟練者の技術伝承を成功させるポイントについてお伺いしてきました。
【Q1】熟練者の技術伝承の難しさはどのあたりにあるのでしょうか?
八重島様)
日本の製造業における「熟練者の技術伝承」の難しさについては、3つポイントがあると思います。
1.熟練者の頭の中の知識やノウハウは共有が困難
1つ目は、「技術」という目に見ない資産は、他者と共有するということが非常に難しいということです。
「技術」は多くの知識やノウハウ、そしてその人の能力の集合体として存在しており、その知識やノウハウそのものは言語化しにくい「暗黙知」としてあります。
「暗黙知」を共有するためには、それを言語化するなど「形式知化」を行う必要がありますが、この作業が非常に難しいのです。
まず、多くの「暗黙知」を所有している熟練者自身が、何が伝えるべきノウハウなのかが分かっていないという事があります。また、伝承すべき事が明確であったとしても熟練者の頭の中が体系的に整理されていないため、それを上手く「形式知化」して伝える事が難しいのです。さらに、上手く文書化するなど「形式知化」したとしても、その情報を伝達するだけでは、相手がその「技術」を駆使し、活用できる訳ではありません。
この例としてよく知られているのは、自転車を運転するという技術の例です。自転車を運転する方法について、もし運転できる人が知り得る知識を言語化して伝えたとしても、運転できない人が運転できるようにはなりません。
つまり、その「技術」はその運転できる人が経験してきた過程で獲得したものであり、同じ経験をしない人には、その「技術」に関する「知識」を伝え理解させることはできても、「技術」を伝承できたとは言えないのです。
2.伝承する対象が要素技術に偏っている
2つ目は、課題解決・価値創造のため、いかに要素技術を活用するかということの重要性があまり理解されておらず、伝承する対象が要素技術に偏ってしまっているということです。
これはどういうことかというと、日本の製造業における「技術」と言えば要素技術と呼ばれる基礎的な「技術情報」を示すことが多く、この情報を伝承することが技術伝承である、と考えられがちで、これらの「技術情報」の真の価値を引き出して資産化するには、複数の「技術情報」を学び分析することに加え、これらを組み合わせたり、応用できるようになる必要があるのですが、この様に統合するスキルが日本の製造業では軽視されがちです。
この統合するスキルを「技術リテラシー」と呼ぶとき、「技術伝承」の成否がその「技術リテラシー」のレベルに大きく依存するということです。「ITリテラシー」という言葉に置き換えて考えるととても分かりやすいと思います。現在はインターネットの発展により多くの人が多くの情報を獲得するコストが大幅に減りました。にも拘わらず皆がそこで得る情報を上手く活用できるかといえばそうではありません。そこには「ITリテラシー」の差が如実に現れます。
つまり、「熟練者の技術伝承」を成功させるためには、「技術」を伝承する側、される側双方の「技術リテラシー」を向上させることを同時に行う必要があります。
なお、余談ではありますが先ほどの「技術リテラシー」について、技術立国であるはずの日本が実は上記に記述した「技術」もしくは「技術を活かして価値を引き出す」ということについて、他の先進国に比べて体系的な教育を受けていないという事実があります。この課題が、「要素技術」開発としてリードした日本製造業が、それらの要素を統合した製品、ビジネスという領域で後塵を踏む結果となる一つの原因だと思われます。
3.既存ビジネスへの影響面から批判的な意見が出やすい
3つ目は、現状のビジネスと並行して「熟練者の技術伝承」に取り組むことになるので、どうしても現場からの反発を受けやすい傾向にあると言うことです。
業務改善活動など何か新しい取り組みをする時と同様に、「熟練者の技術伝承」を推進する際にも、現場からは少なからず反発が出ることでしょう。既存ビジネスを効率的に実行したいと考えている現場にとって、新しい取り組みは新たな負荷や業務的な制約を受けるため、どうしてもストレスを感じて非協力的、批判的な意見が出てきてしまいます。
現場にもこの活動の意義としてビジネスを強靭なものに変えられること、それは回り回って現場にもメリットが生まれることをうまく伝え、一定の理解を得ることが対策のひとつとなります。トップダウンの活動だから従わないとダメだといった一方的な推進は、現場のさらなる反発を招くので避けるべきです。
- この忙しい時期に、その様な活動に時間を割いている暇はない
- 今までで上手く業務を進められているのに、何故その様な活動・業務をしなければならないのか
- 現状でも、業務の中で「技術伝承」はできている。新たにやる活動に我々のメリットを感じない
- 製品開発はマニュアル的な業務ではない、その様な活動は技術者が考えないことに繋がる
このような意見は、現場を担っているマネジメント層、リーダー層が特に強く感じていることで、それは「熟練者の技術伝承」という活動を庇護すべき経営層にも伝播していきます。最終的に経営層というオーナー不在の活動となってしまうと、この活動は失敗という結果に取られかねません。
この3つ目の論点は、「熟練者の技術伝承」というテーマに関わらず、様々な改革を推進する上で共通となる難しさではありますが、これは1つ目、2つ目の「熟練者の技術伝承」というとらえどころのない活動の難しさに輪をかけて、この活動を難しくさせるのです。
- 熟練者自身が何がノウハウなのかを分かっていない
- 熟練者の頭の中が体系的に整理されていないため、伝えたいことを上手く伝えられない
- 技術情報の伝達のみにとどまり真の情報価値を引き出せない
- 技術情報を組み合わせたり応用するスキルが軽視されがち
- 既存の業務を重視する現場から反発を受けやすい
【Q2】よくある技術伝承の失敗例/失敗談を教えてください
八重島様)
「技術伝承」という課題に取り組む活動をしている企業ならば、そのほとんどが非常に有意義な活動をしていますし、決して無駄にはならないことをしていますので、一言で失敗と言い切ることはできません。
しかし、我々はもっとその活動を継続的に活性化させて欲しいと常々感じておりますので、ここではその様に感じた例を挙げてみたいと思います。
例1.技術系文書を探しやすくする仕組みを作るだけに留まっている
過去に作成した設計成果物が紙のまま個人持ちファイルに閉じるといった管理をしている企業ならば、その情報を電子化し、一元管理し、何かあった時にすぐに見つかるようにしたいと考え、その様な情報管理基盤を構築すると思います。
この活動は、本来やらなければならない品質文書の管理そのものであって必要な取り組みではありますが、それをやることが「熟練者の技術伝承」という課題を解決できると勘違いしているケースが多くみられます。
例2.熟練者の知識を文書化するだけに留まっている
これは「熟練者の技術伝承」という言葉から想起される通り、素直に熟練者の知識を文書などに落とそうというコンテンツ作りの活動となっているケースです。これだと、文書を作ることが目的となりがちで、活用することは現場任せになることがあります。
この様な活動に留まってしまうと、せっかく時間を掛けて作ったコンテンツの内容是非を問う「評論家」が多くあらわれ、活動成果が出ない事の戦犯を「技術」という資産を提供した側に押し付ける事に繋がりかねません。
その様な事にならないとしても、せっかく作ったコンテンツを使わない、(大変なので)コンテンツの作り手が他に出てこないなどの状況に陥り、「有意義な活動だったにも関わらず、活用されない事で成果に結びつかなくて上からの評価が低い」という結果になりがちです。
実際に、「技術伝承」という活動を継続的に行えている企業は少なく、その様な活動を一時期したとしても、せっかく作ったコンテンツが徐々に実態と剥離してきて形骸化してしまっているというケースが多くみられます。
例3.熟練者が若手をOJTで教育するだけに留まっている
熟練者が教育のためのコンテンツを作ったり勉強会を開いたりして、若手がそれを教育の一環として受けるようなケースで、OJTによる技術伝承も基本的にはこれに当てはまるパターンの一つです。この様な活動は製造業ならば必ずすべき活動であり、我々がご支援する際にもその施策としてよく挙がるものでもあります。
しかし、結局は「教育がOJT頼り」という、従来通りのやり方から変えられていない状況とも言えます。言い換えると「人から人への属人的な技術伝承」であり、悪く言えば「長年かけて後継者を育成する徒弟制度」の様なやり方に近いとも見えます。
もちろん、これらの教育的な活動すらしない企業の方が危険ですが、「熟練者の技術伝承」というテーマに対策していると思っているならば、この活動だけに頼り切ってしまうのは少し危険な兆候だといえます。
「熟練者の技術伝承」が何故重要課題なのか、その課題に対策するとはどういうことなのかをもう一度考えて欲しいと思います。
- 熟練者のノウハウを文書化するだけの技術伝承取組み
- 散在する技術文書が探しやすくなればいいと思っている技術伝承取組み
- OJT頼りの技術伝承取組み
【Q3】その失敗の原因はどのあたりにあるのでしょうか?
八重島様)
一言で言うと「今までやってきている技術伝承のやり方で十分だ」という意識がある事が原因だと感じております。そういう意識となる根っこには「従来型の開発業務から変わらなければ生き残れない」という危機感の欠如があるのではないでしょうか。
もし、以下の様な状況がまかり通っている様ならば要注意です。
- 基本的には社内や部内など、ある組織グループに閉じた技術伝承である
- 組織の人材構成は階層的にあり基本的に世代が上から段階的に構成されている中で、技術伝承の方向は上から下への一方向で行われる
- 技術伝承の手法は、OJTの中で同じ経験をしながら相手に内在化させる手法に頼り、そのやり方などの裁量は教える側に委ねている
- 開発業務が従来から変わらずに、「技術伝承」はその余剰時間、余剰人員でやる位置づけとなっている
この様な考えや手法は、高度成長期の製造業に見られる終身雇用を基本とした人事評価制度の中、一方向に組織が大きくなり連続的な成長を実現してきた時期には非常に上手くいったのですが、ビジネス環境が変わる中で従来のやり方が通用しなくなってきていることが「熟練者の技術伝承」の難易度を高めており、多くの企業から課題として挙げられている背景としてあります。
昨今、製造業を取り巻く環境として「深刻な人材不足の恒常化」があり、そうなると人材の流動性も高まります。また市場環境変化や技術発展も非常に早くなってきており、従来のように数年かけて同じ業務を経験させながら「技術伝承」を行う事が困難になってきております。
この様な状況に対応していくためには、従来成功したやり方に固執せず、その手法を更に進化したものに変えていかなければなりません。その為にも「技術伝承」というテーマに対して危機感ともいえる課題認識を経営層やマネジメント層がもち、その様な彼らの庇護のもとで、現場は新たな手法を業務に愚直に組み込んでいく活動を回せる様にしていかなければならないと思います。
そして、その活動が組織に閉じず、その活動成果を全体としての組織力向上に繋げるために、それらをいかに統合し、最適化していくかが重要となります。
- 今まで通りの技術伝承のやり方で十分だという意識がある
- 現場は技術伝承ができていると思い込んでいる
- 現場にもメリットがあることをうまく伝えられていない
- 活動のオーナーである経営層が不在な状態になっている
【Q4】どのようなことに注意して進めると良いでしょうか?コツやポイントがあれば教えてください
八重島様)
1.「技術」という見えざる資産を統合し、組織として共有するために「設計プロセスの可視化・共通化」から始める
「技術」という見えざる資産を組織的に活用、再利用するためには、「技術」を構造化した情報として整備する必要あります。そのためにも、「技術資産」を受けるための全体像としての枠組みを定義する事が重要となります。
その全体像は、組織構造、技術体系、製品体系、業務構造という従来からマネジメントしているものが重要なのはもちろんのこと、それよりも粒度を細かくする必要があります。つまりは、設計者が設計を進める上での「設計プロセス(思考プロセス)」を全体像の枠組みとして定義すべきです。そして設計プロセスの構造に、熟練者のもつ一番重要な知見である「設計思想」を組み込み、それを組織の資産にする必要があります。
この「設計プロセス」に対して、各部署の成果、例えば図面や技術仕様書、さらには設計根拠や設計基準を紐づけて蓄積していくことで、今までバラバラに管理していた様々な情報が、洗練された「熟練者の設計思想」を元に統合されることに繋がります。この「技術資産」を統合するための「設計プロセス」のことを我々は、設計を抽象化(モデル化)したものということで「デザインモデル」と呼んでおります。
2.「設計プロセス」の可視化や、それの活用、メンテナンスを「技術リーダー候補」ができるようにする
「技術資産」は蓄積するだけでは効果は出ず、活用することで初めて効果が出ます。「技術資産」を組織的に活用するために、それをけん引する役割を担うのは、多くの技術要素を統合し、ひとつの商品に統合する役割を担う「技術リーダー」と呼ばれる人財です。つまり、組織的な「技術リテラシー」を向上し、技術資産の活用を促進する中で、「熟練者の技術伝承」を実現させられるかは、次世代を担う「技術リーダー候補」に掛かっています。
ただし、彼らは忙しい中で従来通りの開発業務や手法を駆使しビジネスを回しています。急に新たな手法に切り替えるのではなく、彼らの「技術リテラシー」を向上させるための教育的な取り組みみを組み込むことも重要になります。
3.小さな効果を創出しながら、徐々に理解者を増やして活動の範囲を広げていく
組織の技術を活用する力「技術リテラシー」は急には上りません。技術を可視化・統合・再構築する手法を学び、それを実践しながら技術資産を蓄積するなどを経験する中で、組織力が向上していき、次世代型業務に変わります。その中で、製品開発のタイムスパンと、技術資産管理強化や技術伝承のスパンに違いが産まれます。にも関わらず、製品開発よりも短期的な指標で投資対効果を判断する様なマネジメントや意思決定を経営層がしてはいけません。
この様な長中期的なスパンの投資に対しては、大きな方向性を示しつつも、小さく軌道修正を行いリスクを最小化するマネジメントが重要となります。そのことを経営層が理解するのみではなく、現場にも理解をさせ、現場主導で着実に進化を進められる様にできるかが成否を分けます。
この活動を進めていく過程で、目的を達成するために既存の仕組みや業務ルールを変える事も必要になります。しかし、既存の業務や仕組みを変える際には必ず多くのコンフリクトが現場に起きます。このコンフリクトで活動がつぶれない様にするためにも、活動しながら簡易的に検証し、進化させていくことが望ましいと思います。
- まず「技術」という知的資産を統合する「設計プロセス」のモデルを獲得する
- 上記のモデルを整備・活用する技術の教育を「技術リーダー候補」に行う
- 小さな効果を創出しながら、「技術伝承」の活動を進化させる進め方を指向する
【Q5】技術伝承はすべて自力でできるのでしょうか。特にサポート/ツールが必要な部分を教えてください
八重島様)
全て自力で行うという制約があると、自分たちが知り得る知識や技術のなかでできる活動となり、「従来型の開発業務、技術伝承手法から変えらない」に帰結してしまいます。
ここで、「技術伝承」や「技術資産の活用」の手法そのものも「技術」であることを強く認識し、世にある最新技術やそれを駆使する外部人材を活用することを検討した方が良い。つまり技術を扱う手法や製品開発手法そのものも、オープンイノベーションを行えることが望ましいのです。
- 「技術を可視化・活用する手法」の習得と、自社に合わせた最適化
- 技術資産を統合するための「設計プロセス」のモデリングツール
- 「技術伝承」という活動を効果に繋げるためのプランニングと実行支援
- 暗黙知の可視化だけなら自力でできなくはないが、継続すること、再利用が可能な技術資産とすることを考えると専用のツールを利用することが望ましい
- 自力では内部の利害関係などで頓挫するケースが多いため、外部の者が推進した方がスムーズに進む点が多い
【Q6】サポートしてくれる専門家を選ぶ際のポイントを教えてください。またワイ・ディ・シー様の場合はどんな特徴がありますか?
八重島様)
まずは「技術を可視化・活用する手法」に対する方法論を持ち、それを駆使できる専門家であること。製品開発プロセス改革や、設計標準化・モジュール化などの手法への応用実績もなければ、ただのナレッジマネジメントやPDMツールを理解しているだけとなり物足りない。そして、「従来型の開発業務、技術伝承手法」から変わるためには、人は上記の知見では足りず、皆が目指すべき姿を描き、そこに向けたプランと現場を変えるための「チェンジマネジメント」を駆使した実践支援ができる、「コンサルティング」としての力量も重要となります。
最後に、近年の動向としてモノづくりもデジタライゼーションに対応し、生産性向上や効率化を実現する必要があります。この様な進化へとつなげるには、IT技術の専門家や、AIやデータアナリストに関する専門家サポートもあるのが望ましいと思います。IT技術といっても広いですが、特に軸となる「設計プロセスのモデリングツール」や、それを活用した技術情報や製品情報を管理する仕組みの構築に関する領域の専門性が必要です。
ワイ・ディ・シーでは、DCM領域の改革を専門とするコンサルティングチーム、IT技術やAI専門家を有しております。システムやツール販売を目的とせず、企業変革や進化を目的とした統合的なアドバイスや支援が可能です。
また、コンサルティング支援時に活用していたコンサルティングツールやテンプレートを汎用化し、設計プロセス専門のモデリングツールとして開発した「iD Suite」の販売やトレーニングサービスも開始しました。他の汎用的なツールを活用するよりも、重要な成功要素をデータ視点でも抑えた活動が容易となります。
- 技術を可視化・活用する手法に対する方法論を持っている
- その方法論を駆使してプロジェクトを支援できる専門家である
- プロジェクトの目指すべき姿を描くことができる
- チェンジマネジメントを駆使した実践支援ができる
- 技術や製品情報を管理する仕組み構築の領域に精通している
【Q7】最後に八重島様の所属されている「共動創発」について教えてください
八重島様)
我々は、製造業の開発設計領域を軸に、いかに製造業の競争力を高めるか、製造業が創造し提供する顧客価値を最大化するか、をテーマとする改革支援をさせて頂いております。
開発設計領域を軸とした改革の特徴としては、「知識」もしくは複数の知識やノウハウ、能力が組み合わさった「技術」という見えざる資産をいかに、属人的な資産から組織資産に置き換え、その資産を有効活用することで新たな提供価値を創造し、顧客に提供することで新たな価値を産み出すかという視点で製造業の改革を推進しております。
つまり技術を企業活動をする上での重要な資産としてみた時に、いかにそこからの生産性を向上させるかという視点でビジネス活動を見るのが、DCM領域からの改革を専門とする我々の特徴です。
本日はお忙しい中インタビューにお答え頂きありがとうございました。
(可視化ノート編集担当 N.I)
その他、製造業の技術可視化について知りたい方はこちら
【無料資料ダウンロード】株式会社ワイ・ディ・シー様ご提供